- HOME
- Beyond X 最前線
- 世界に認められた日本国内の3つの工場とは
世界に認められた日本国内の3つの工場とは
グローバル・ライトハウス・ネットワークとは
世界経済フォーラム(The World Economic Forum:WEF)は、デジタル技術などを活用した先進工場や企業を認定するプログラム「グローバル・ライトハウス・ネットワーク」(Global Lighthouse Network:GLN)を展開している。
このプログラムは、米国のマッキンゼー・アンド・カンパニーと共同で2018年に発足した。測定可能な1000件を超える製造現場を調査し、「テクノロジーを活用してパフォーマンスと持続可能性にプラスの影響を与えながら第四次産業革命をリードし、財政面に限らず運用面でも成功した世界で最も先進的な工場」を「Lighthouse」(ライトハウス)として認定する。
2024年には22の工場が「Lighthouse」に認定
2024年は新たに22の工場が加わり、これまで170以上の工場が「Lighthouse」に認定されている。2024年に新たに加わった「Lighthouse」では、インタラクティブなトレーニングプログラム、スマートデバイスやウェアラブル端末、ロボット工学、AI、マシンビジョンを組み合わせた自動化システムなどのデジタルソリューションにより、労働生産性が平均50%向上したという。
また、プロセスモデリングと根本原因分析により、「Lighthouse」のエンドツーエンドのサプライチェーン全体で効率性が向上し、エネルギー消費を平均22%、在庫を27%、スクラップや廃棄物を55%削減している。
「Lighthouse」に認定された工場は、革新的な第四次産業革命(4IR:The Fourth Industrial Revolution)を導入していることがポイントだ。4IRでは、人工知能(AI)、IoT、ロボティクス、3Dプリント、ブロックチェーン、ビッグデータ、デジタルツインなど、高度なデジタル製造技術を融合させている。
2024年に認定されたアストラゼネカ(スウェーデン、セーデルテリエ)では、生産能力の向上と新製品発売の加速化を図るため、機械学習や最適化アルゴリズムを含む50以上の4IRソリューションを導入。これらの取り組みと3,000人の従業員のアップスキリングにより、労働生産性は56%増加し、新製品の開発リードタイムは67%短縮したという。
同じく2024年認定のコカ・コーラ・シンガポールでは、機械学習を活用した需要予測、ロボット工学、高度なスケジューリングアルゴリズムを導入。これにより、処理能力は28%向上し、労働生産性は70%向上、欠品は80%削減、時間通りの配送は31%改善する一方、スコープ2排出量は34%削減された。
同様に2024年に認定されたジュビラント・イングレビア(インド、バルーチ)は、特殊化学製品のグローバルな既存製造拠点に4IRテクノロジーを導入し、2,000人以上の従業員にリスキリングを実施。AI、機械学習、IoTベースのデジタルツイン、予測プラットフォームを活用した30以上の統合ユースケースを通じて、全体的なプロセスのばらつきを60%削減し、生産量を倍近く増加させたという。
3つの工場が「持続可能性ライトハウス」に認定
また、2024年には22の工場のうち、先進技術を活用して環境への影響を低減する3つの工場が、「持続可能性のライトハウス(Sustainability Lighthouse)」に指定された。
フォックスコン・インダストリアル・インターネット(中国、深セン)は、カーボンニュートラルという家電業界の公約を達成するために、AI、IoTその他の4IRテクノロジーを活用し、リサイクルの最適化、二酸化炭素排出量の追跡、持続可能性のためのイノベーションを実現した。これにより、スコープ3の排出量を42%削減し、スコープ1および2の排出量を24%削減。また、リサイクル材料の含有率を55~75%に増加させたという。
青島ビール青島工場では、高度なアルゴリズムとIoTを活用し、ビール生産におけるエネルギーと炭素強度の削減を目的とした25のユースケースを展開し、単位エネルギー消費量を25%削減し、スコープ1および2の排出量を57%削減、スコープ3の排出量を13%削減したという。
日本ではこれまで3工場が認定
日本では、日立製作所 大みか工場、GEヘルスケア 日野工場、P&G 高崎工場の3ヵ所が「Lighthouse」に認定されている。
GEヘルスケア・ジャパンは、GEヘルスケアの中核拠点の1つとして1982年に創設。予防から診断、治療、経過観察・予後管理までをカバーする「プレシジョン・ヘルス」の実現を目指し、インテリジェント機器やデータ分析、ソフトウェア、サービス等を提供している。
日野工場は、最新のデジタル・テクノロジーを用いてリアルタイムでデータを活用し、製造オペレーションからサプライチェーンまで全体を最適化することに率先して取り組んだ。同社では、さまざまな最新の技術を活用して新たな改善点を発見し最適化を図ったうえで、顧客に提供する「品質」「納期」「コスト低減」といった価値を最大化する取り組みが、「Lighthouse」に認定された理由だと考えているという。
P&G高崎工場は、製品開発から販売までのバリューチェーン全体において、デジタルツイン、データコネクティビティ、AI、機械学習など、先進のデジタル・テクノロジーを活用しており、第四次産業革命を牽引する先進工場となっている。同社は、これらの技術革新により、製品開発期間や試作のための操業停止日数の短縮化、流通業パートナーの発注利便性の向上、および生産能力の向上を実現し、さらに生産性の改善と市場ニーズに応える迅速な対応を可能にしたことが評価され、「Lighthouse」の選定に至ったと考えているという。
日立製作所 大みか事業所は、情報制御システムの開発・製造・品質保証から保守までの一貫体制を構築し、バリューチェーン全体の最適化を志向している。その中でも、「Lighthouse」選出時にWEFに訴求した特徴的な取り組みとしては、大きく5つのポイントがあるという。
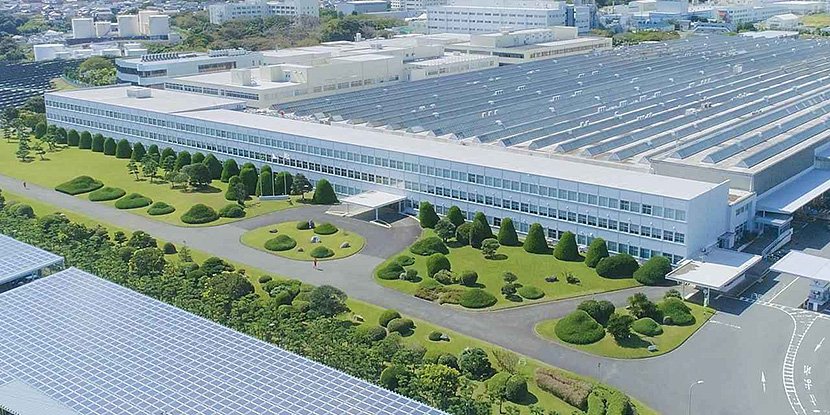
日立製作所の大みか事業所(出典:日立製作所)
第一のポイントは、ハードウェアの設計・製造において現場の4M(huMan(人)/ Machine(設備)/ Material(モノ)/ Method(方法))データを活用し、生産リードタイムの短縮などを実現した「高効率生産モデル」を確立したこと。
第ニのポイントは、ソフトウェアの設計・開発フェーズでの「自律分散フレームワーク」によるシステムの高信頼性・拡張性を実現したこと。
自律分散フレームワークは、オンラインでの拡張が可能である「拡張容易性」、システムを稼働させながら保守を行うことができる「オンライン保守性」、不具合時もシステム全体を止めない「高信頼性」、緊急度の高いデータを優先的に処理できる「リアルタイム性」などを大きな特徴とする。
このフレームワークを活用することで、制御システムに求められる品質を満たす信頼性が高いシステムを安定的に開発することが可能となり、大みか事業所では電力や鉄道など約4,000の社会インフラシステムに、このフレームワークを適用。ソフトウェア設計段階の工数削減とともに、急速に変化する市場環境へ柔軟に対応するシステム開発・運用を実現しているという。
第三のポイントは、実稼働中の環境では実施できないシステム試験をシミュレーション環境で実施する「総合システムシミュレーション環境」の活用による徹底した品質管理を行ったこと。
第四のポイントは、顧客のシステム運用・保守を支援する「サイバー防衛訓練検証設備」や「安定稼働サービス」による全体最適化・高度化の取り組み。
そして、第五のポイントが、EMS(電子機器製造受託)・生産計画連動による電力ピークシフト(省エネ)や、太陽光・蓄電池の自立運転によるBCP(事業継続計画)強化で、スマートなエコファクトリーを実現する「環境エネルギーマネジメント」だという。
これまで世界で「Lighthouse」に認定された工場は172ヵ所あり、中国の工場は74ヵ所で圧倒的に多い。日本の製造業は生産性が低いといわれており、認定されたのはまだ3工場のみだが、今後、4IRを活用することで、認定数が増えることを期待したい。
ミライト・ワンのソリューションに関するご質問、ご相談など
ございましたらお気軽にお問い合わせください。
最新の特集
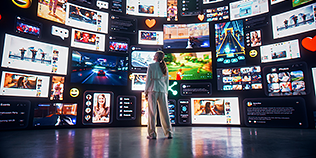
イベント/エンターテインメントDX